By Roma Parikh
Raw sienna is a yellow-brown pigment classified as an earth pigment, originally sourced from Siena, Italy, hence the name. When I first received this assignment to research the earth pigments, I thought it would be horribly boring and repetitive. To some degree, I was correct. After having read multiple sources repeating the basic facts about how earth pigments come from minerals in the ground and include metal oxides, I was quite ready to be done. Unlike the unique recipes used to make verdigris or vermillion (that I previously researched and wrote about here), these earth pigments seemed to offer no surprises and no room for curiosity.
Until, of course, I read about the process to create burnt sienna from raw sienna. The chemical breakdown of raw sienna is about 90% iron oxide (hence the yellow) and secondary quantities of manganese oxide which helps distinguish it from pure yellow ochre. Burnt sienna is created by heating up raw sienna until the heat partially converts the iron oxide into hematite1.
This substance provides the red undertones while the entire pigment takes on a much darker brown. This process is called calcination. Modern day calcinators can heat up products through indirect contact up to temperatures anywhere between 1000 °F and 2000 °F2. It is unclear if medieval pigment-makers burnt the sienna to similarly hot levels as they could not measure the temperature accurately. Moreover, the pigment-makers could not have known that the heating process would lead to a change in color caused by the iron oxide dehydrating and converting to hematite. They didn’t have a periodic table of elements or a sophisticated understanding of chemistry in the 1400’s. So how did they conceptualize this color-change discovery without our modern-day lens?
The answer? Pottery.
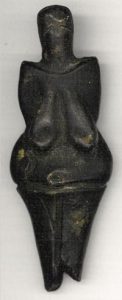
It is a craft as old as time, dating as far back as 25,000 BC3. Wow. By now, the art of pottery-making has become a standardized process. The basic steps can be broken down as such: (1) source the clay, (2) mold and decorate the clay, (3) subject it to extremely high heat in a kiln, (4) glaze, paint, and adorn the end product. The heating process used in pottery is referred to as sintering. It is extremely similar to that of calcination, as my descriptions prove. Since the processes are so similar, medieval pigment-makers likely based off their experiments with heating raw sienna off of the results of pottery-makers heating up different clay products and noticing changes in color, texture, and stability.
Medieval pigment-makers were not thinking in technical terms and chemistry the way I’ve broken down these pigments. Instead of a scientific calculus, they approach it with a much more informal, interdisciplinary, and oral approach. In the case of raw sienna, they took information about the change in color, which seems tangential to the goals of pottery-maker and transform that a ubiquitous and successful pigment. The story of sienna is what has lead me to this beautiful and crucial aspect of the medieval world: more than science, interaction and crossover between disciplines can lead to creativity and innovation.
Of course, the story of sienna does not just end there. It’s popularity has led to its scarcity as natural pigment. The original mines in Siena, Italy were completed depleted of raw sienna by the 1940’s. An astonishing rate of consumption for such a plentiful substance. Since then, similar compositions of raw sienna have been sourced from Sicily and Sardinia as well as Germany’s Hartz Mountains and France’s Ardennes4. However, the colors made from that earth are not as true and pure in hue and texture, forcing many modern pigment-makers to explore synthetic versions. One such example is the company, Winsor & Newton. Up until 1988, they had sourced their raw sienna from a mine south of Siena. In due time, that mine’s stores of sienna were also depleted. At this point, the company tested out the synthetic product. They found it produced a pigment with the exact same transparency and potency as the original sienna. The company now exclusively sells the synthetic pigment, making it harder to find a natural raw sienna pigment.
One of the beauties of pigments, especially natural ones, is to trace their history. The story of sienna threw me entirely off-guard by how interesting and intriguing it became. I found myself far more immersed and entangled in the medieval world than I had ever pushed myself. For something as dull as dirt, sienna has made me reflect and reconsider the way I view the world and the way I learn from history.
Works Cited:
[1] Pigment Compendium: Optical Microscopy of Historical Pigments. Eastaugh, Nicholas, Valentine Walsh, Tracey Chaplin, Ruth Siddall. Pages 367-368.
[2] “Calicination”. Compendium of Chemical Terminology (Gold Book). International Union of Pure and Applied Chemistry.
[3] “The Origins of Ceramic Technology at Dolni Vestonice, Vandiver”, P.B., Soffer, O., Klima, B., and Svoboda, J., Czechoslovakia. Science, Vol. 246, Nov. 24, 1989, pp. 1002-1008.
[4] “Italian Burnt Sienna”, Natural Pigments, https://www.naturalpigments.com/italian-burnt-sienna-1924.html